Project example conception & requirements
"Our goal was to provide the customer with an IT system that optimally supports their production processes and can adapt dynamically to changing processes and changing IT landscapes. With the order management system we developed, together with the customer, we have a modern, created a future-proof and flexible system that makes the manufacturing processes more transparent, efficient and error-free and thus makes a decisive contribution to the success of the company."
Project Manager SWMS
Challenge
Due to company growth and steadily increasing order numbers, the production area is currently being expanded. In this context, the company has dealt with the question of how the manufacturing processes can be better supported and optimized by IT systems than before.
Proceedure
Pain points in production were identified as part of a process analysis based on the plant flow design method. The production orders are currently sent to the various workstations via paper slips. With the current size, this is not a problem at first, the production works and orders are fulfilled. The enlargement of the production area and additional production facilities make the processes so complex in the medium term that a paper-based organization creates an unmanageable effort and is clearly error-prone.
In addition, this is already leading to a lack of information and the following three potential areas for improvement:
- The status of an order is not transparent and can only be researched with a search effort - but the customer asks: Where is my rush order?
- Exact production times for the manufactured products are not recorded, which means that post-calculation of the orders is not possible - Controlling wants to know: What are the manufacturing costs for product A?
- The capacity utilization at the workstations is not known - The production manager plans the production: Can we manufacture 30 additional products next week?
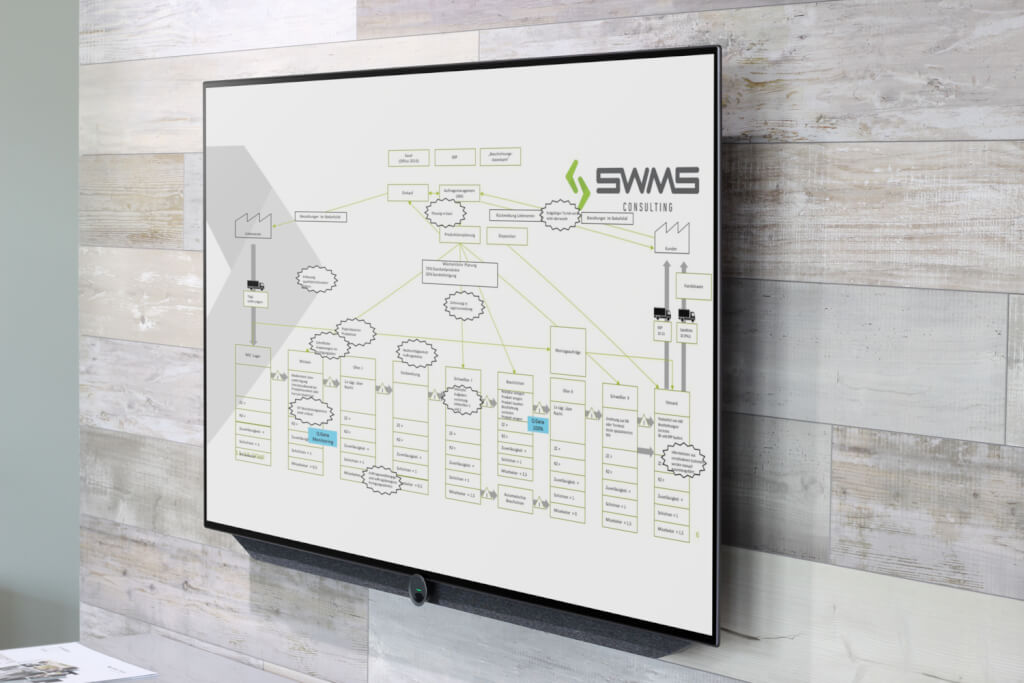
A concept for the company's future IT system landscape was developed in workshops. Standard processes (in this case, for example, sales and accounting) are covered by a standard solution. The customer already operates an ERP system for this purpose, but is also discussing a new implementation project. On the other hand, individual processes (among others the processes in production) should be supported by an individual solution that is developed together with SWMS. There should be no costly adaptation of ERP system modules or the introduction of a monolithic MES system. Rather, a system is being developed that optimally supports the existing manufacturing processes and that can be dynamically adapted to changing processes and the changing IT landscape in the future. The starting point is digitized order management and production data acquisition in production, which means that the potential mentioned above can be achieved.
Result
In close cooperation with the customer, an order management system is developed that orchestrates modern IT technologies. The user interface is based on a low-code platform, which can be used to quickly design interfaces that precisely cover the information requirements at the respective workstation. Another advantage of low-code: After a short introduction to the system, the customer can later make simple changes to the user interface independently and thus adapt it iteratively to his production requirements. In addition, the system is based on a noSQL data structure in the backend, which means that the system can adapt to changes in the process flow (e.g. adding or removing work stations and process steps as well as the collection of further data). In this way, events can be recorded at the workstations, which are then evaluated with regard to the capacity utilization of the station, the processing time and the order status. In addition, the system can be gradually expanded, controlled by the customer's needs, with additional services and classic MES functions that support evaluation, information provision and production planning.